Paving the Way for a More Efficient Travel System
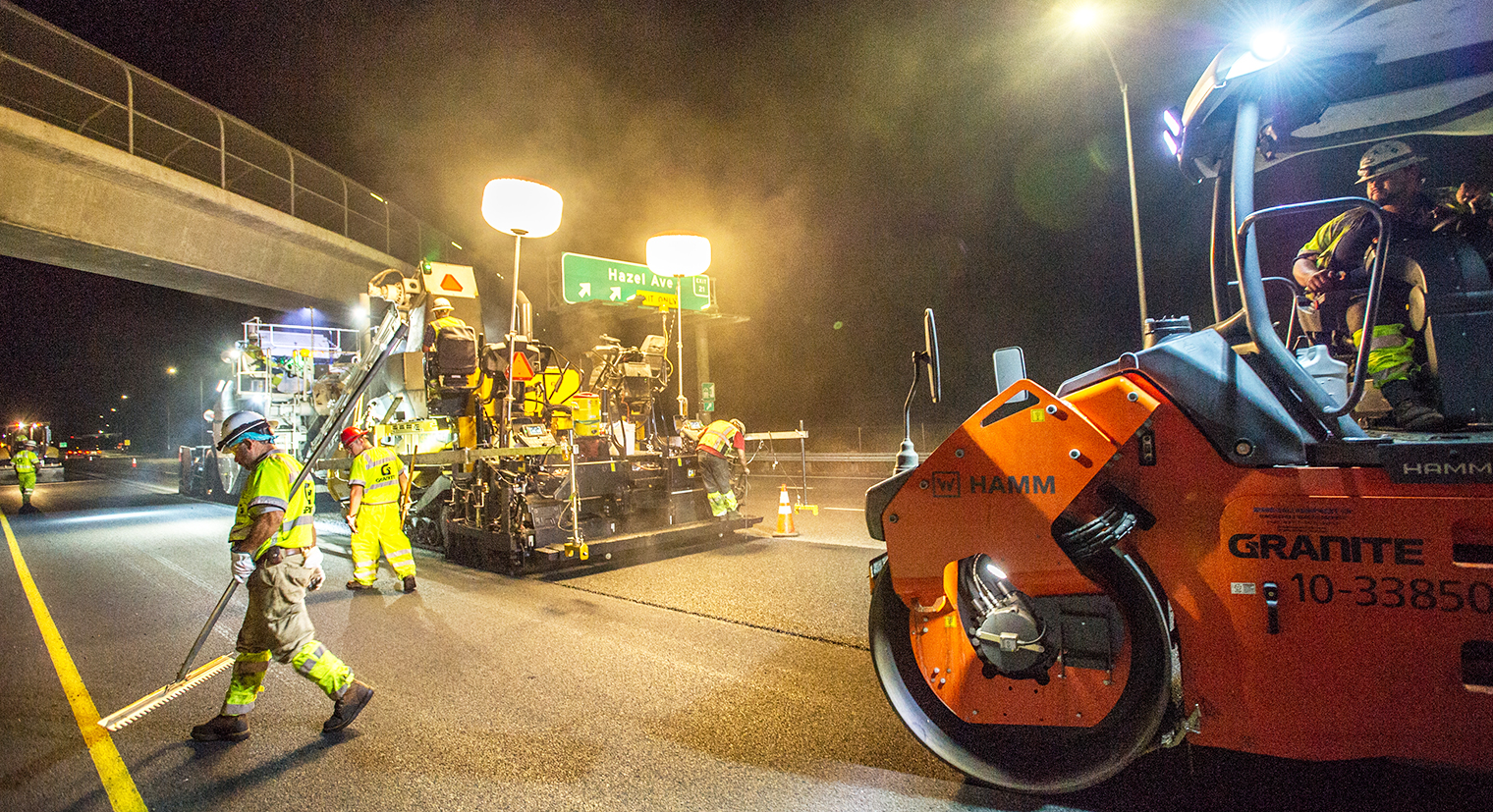
Caltrans Finds $340 Million in Cost Savings/Avoidances in Latest Fiscal Year
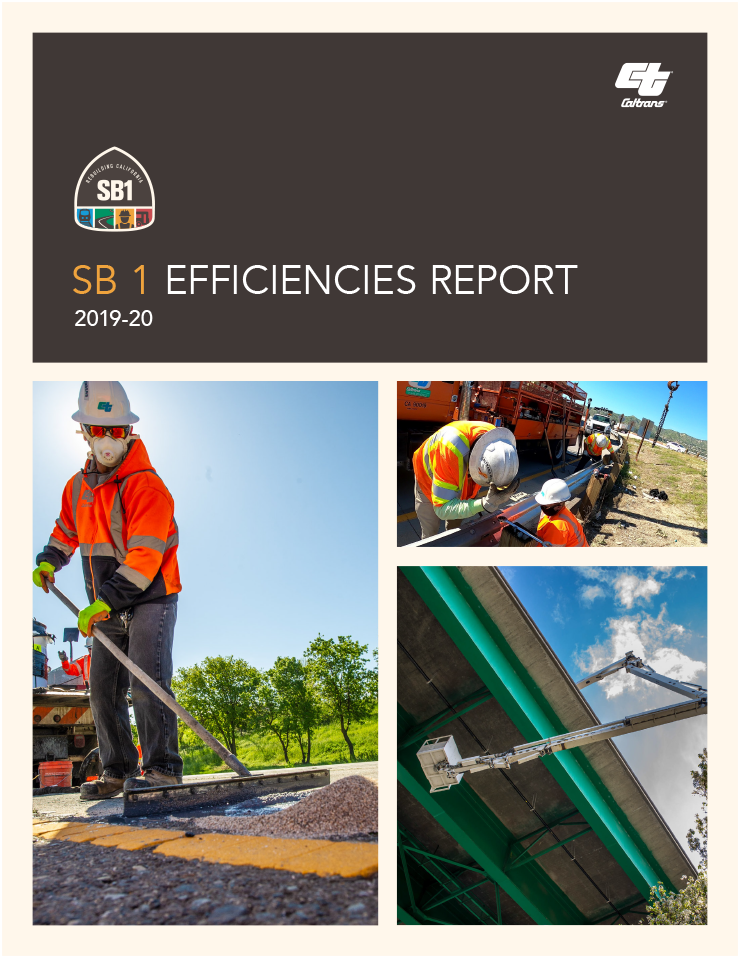
Caltrans continues to realize cost-saving efficiencies in its operation of the State Highway System, with savings reinvested in maintenance and rehabilitation needs across the state.
Caltrans identified $340 million in cost savings and avoidances during the 2019-2020 fiscal year, outlined in its annual report required by SB 1, the Road Repair and Accountability Act of 2017. Of that amount, Caltrans listed $174.3 million in new efficiencies achieved through improved operations and innovative methods. Recurring efficiencies, practices begun in previous reporting years, yielded an estimated $20.5 million in cost reductions or savings. Another $145 million in savings or costs avoided through additional measures was not counted toward the SB 1 efficiency goal, but listed nonetheless because the steps taken represent strategic efficient investments.
The landmark transportation funding law requires Caltrans to become more efficient with the taxpayer funds it spends, and find ways to save at least $100 million each year.
Even though Caltrans has been delivering projects more efficiently for many years, fiscal year 2017-18 was the first time that efficiency measures were monitored, quantified, and reported due to SB 1.
The first annual efficiencies report identified $133 million in avoided or reduced costs, achieved through process improvements, new technology and innovative project delivery methods. The 2018-19 report listed $233 million in implemented efficiencies.
The 2019-20 fiscal year was the third straight year that Caltrans exceeded the goal of $100 million in annual savings set by SB 1. Caltrans reported 10 new and seven recurring efficiencies, and the savings wrought from those improvements will be reinvested in the maintenance and rehabilitation of the State Highway System.
The new efficiencies yielded $174.3 million in estimated dollar savings achieved/avoided. Listed in order of savings, they are:
Stormwater Mitigation — $85.7 million
Use of a particular kind of pavement along one stretch of highway allowed Caltrans to keep roadway pollutants from washing into the surrounding landscape during rainstorms and eliminated the need to install costly treatment devices along the right of way. A multiyear study conducted by Caltrans showed that the porous asphalt mix — known as open-graded friction course — captured contaminants that run off with water, as well as improved drainage, reduced road noise and increased driver visibility by reducing road spray. See sidebar story below for more details on this efficiency.
Project Bundling — $40.2 million
Caltrans bundles projects to combine work types — including design, preservation, rehabilitation, or complete replacement — that can be tiered, have an overlap and involve similar scopes of work. In 2019-20, Caltrans bundled 30 projects at the construction stage into 14 contracts that cumulatively trimmed about $40.2 million in potential costs.
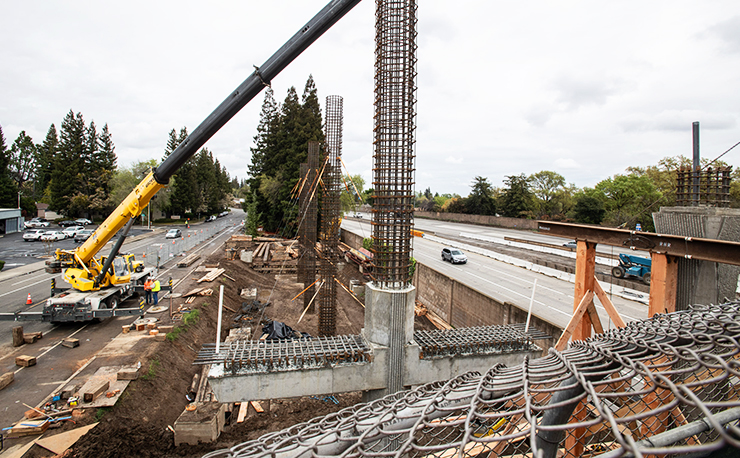
Long-Life Pavement — $37 million
An Interstate 5 rehabilitation project in Sacramento is benefitting from advances in pavement technology thanks to a longstanding partnership with the University of Davis Pavement Research Center. Using a new approach in materials and structure design, the FixSac-5 project is rolling out a new road surface with a 60-year pavement life projected to save $37 million over its anticipated lifespan.
Automated Machine Guidance — $5 million
This technology uses global positioning system (GPS) devices and rotating laser levels that allow bulldozers, blades, scrapers, and paving machines to achieve greater accuracy. In 2019-20, Caltrans completed 20 projects, an estimated combined volume of 3.5 million cubic yards of earthwork, using Automated Machine Guidance.
X-ray Fluorescence Technology — $2.4 million
Called XRF, this technology is housed in a handheld tool that evaluates total lead concentrations in seconds, providing a less costly alternative to laboratory analysis. XRF technology was used on 48 projects involving 1,638 boreholes, eliminating consultant costs.
Independent Assurance Program — $1.8 million
By consolidating the functions of a quality assurance program for construction projects, 11 fewer positions were needed.
On-Call Culvert Service — $800,000
Reducing the number of individual culvert lining projects into an on-call contract reduces in-house surveying and engineering support costs.
Unmanned Aircraft Systems — $682,000
Caltrans is increasingly using drone aircraft for surveys, bridge inspections, construction monitoring, emergency response, field investigations and media support. Drone missions on three major construction projects helped avoid costs.
Project Initiation Proposal Improvements — $663,000; Program Supplement Agreements — $10,000
Caltrans’ Lean Six Sigma process contributed to procedural improvements for both areas of work.
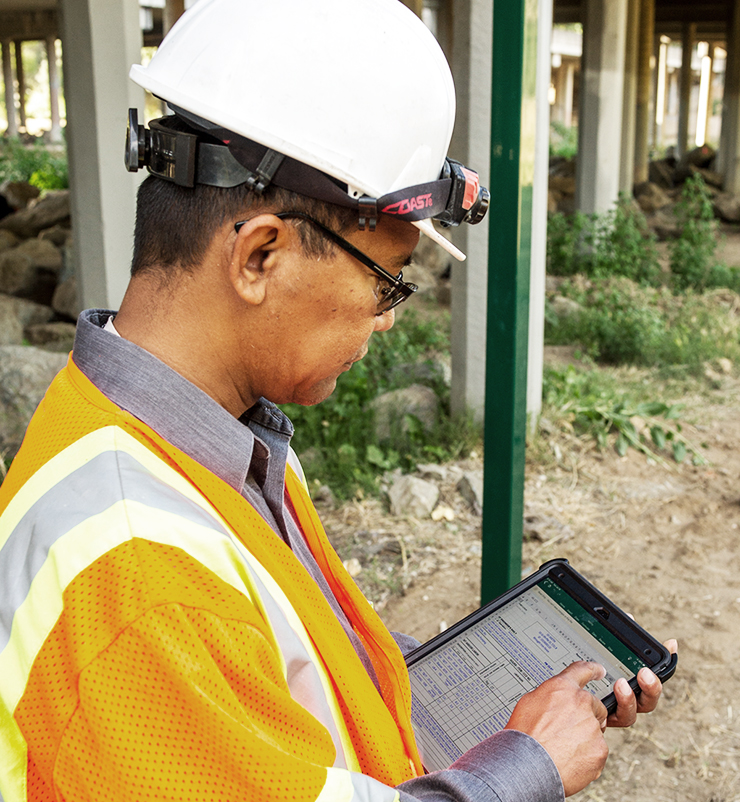
Recurring Efficiencies
Seven continuing practices are yielding cost reductions or resulting in money not spent, saving an estimated total of $20.5 million for highway improvements, according to the efficiencies report. These include:
- highway lighting LED retrofits, $6.4 million;
- high-reflective, more durable striping material, $5.1 million;
- value engineering change proposals, $4.2 million;
- mobile field devices, $2.6 million;
- GPS devices in fleet, $1.9 million;
- high-performance reflective signs, $226,000; and
- bundling of advance mitigation credit purchases, $52,000.
Additional Efficiencies
In addition to new approaches, Caltrans continues to benefit from process improvements put in place in earlier years. The prior strategies yielded $145.3 million in cost reductions/avoidance in FY 2019-20, the report said.
Chief among those efficiencies:
- Value analysis study, $72.5 million. Eight projects in 2019-20 used this process that assigns teams of subject matter experts early in the project development cycle to analyze function, benefits and cost.
- Construction Manager/General Contractor, $36.4 million. Contractors are brought in early in the project delivery process to work collaboratively with Caltrans on eliminating potential pitfalls, managing costs and improving quality. Once Caltrans and the construction manager agree on a price for construction of the project, and the construction manager becomes the general contractor. Use of this process on two major highway projects in FY 2019-20 was credited with saving $36.4 million thanks to construction-stage innovations.
- Streamlining National Environmental Policy Act (NEPA) review , $21.8 million. By taking responsibility for NEPA reviews of projects, Caltrans expedites the preparation of associated documents and begins project construction earlier. No environmental protection standards are compromised during the process. Caltrans conducted a total of 151 NEPA reviews in 2019-20.
Other ongoing savings were recorded with reclaimed asphalt pavement, $12.7 million; and cold in-place recycling of pavement, $2 million.
Source: SB 1 Efficiencies Report, 2019-20.
Pavement Surface Traps Toxics, Saves Money
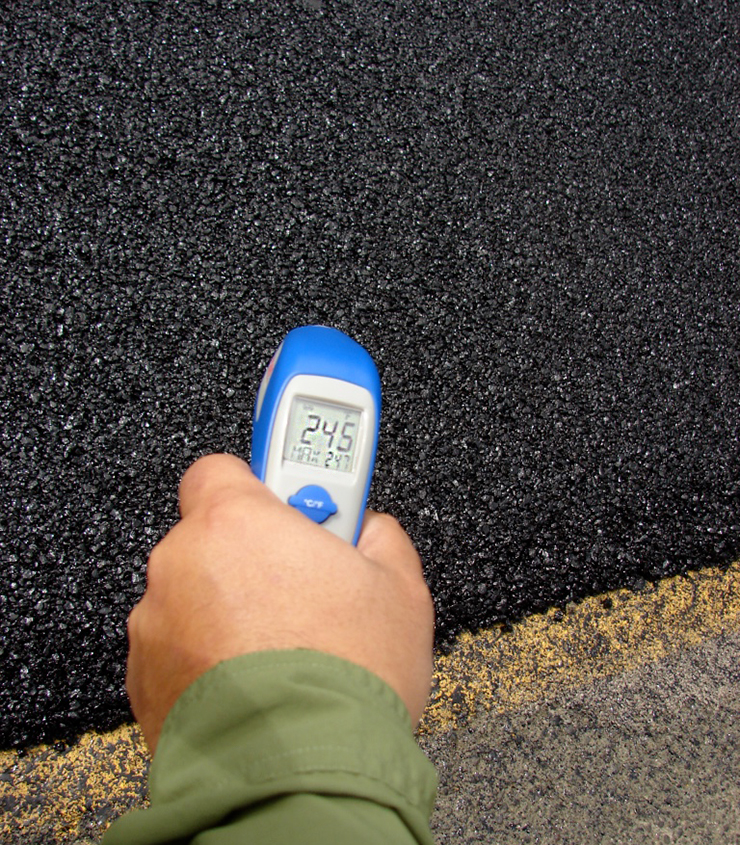
An innovative type of pavement that traps road surface pollutants rather than allowing them to drain off is being credited for saving Caltrans more than $85 million in the 2019-20 fiscal year.
Use of the pavement — known as Open Grade Friction Course (OGFC) — in a watershed area threatened by pollutants spared Caltrans from having to build expensive water treatment facilities to remove toxic metals and sediment from storm runoff.
The $85.7 million in estimated cost savings was the largest of the efficiency measures identified in Caltrans’ report on ways it has saved money or avoided operational costs in FY 2019-20.
Caltrans earlier conducted a multiyear statewide field study that confirmed OGFC pavement is effective at removing pollutants from stormwater runoff, in addition to improving drainage, reducing spray and splash that impair driver visibility, and lowering road noise. When stormwater carrying toxics flows through the voids of the porous OGFC pavement, the study found, pollutants are caught, and cleansed stormwater discharges from the pavement.
After the study was completed, the State Water Resources Control Board granted stormwater treatment credits for Caltrans’ use of OGFC pavements in a 530-acre area where nearby waterways have been compromised by pollutants.
The state board’s approval of credits for OGFC freed Caltrans from having to construct expensive roadside treatment facilities to contain toxics from tainted stormwater. On average, Caltrans spends about $176,000 per acre in construction capital costs to treat stormwater runoff in its rights of way. When multiplied over a 530-acre area, the use of OFCG pavements saved more than$93 million in treatment costs. Caltrans spent $7.5 million in study costs, and reinvested $85.7 million in other repair and rehabilitation projects on the State Highway System.
The innovative method of removing roadway pollutants before they reach California waters shows that Caltrans is committed to being a good environmental steward, and ensures water discharged from the State Highway System is treated properly.