Chapter 6: Sampling and Testing, Section 2: Acceptance of Manufactured or Fabricated Materials and Products
- 6-201 General
- 6-202 Responsibilities for Acceptance of Manufactured or Fabricated Materials and Products
- 6-203 Manufactured or Fabricated Materials and Products Acceptance
- 6-203A Source Inspection
- 6-203A (1) Inspection Requests and Dispatching
- 6-203A (2) Material Inspection—Sampling and Release
- 6-203A (3) Nonconforming Materials at the Source
- 6-203A (4) Source Inspection Expense Deductions
- 6-203A (5) Source Inspected Materials Acceptance
- 6-203A (6) Materials Manufactured to Caltrans-Specified Formulation
- Table 6-2.1. Inspection of Fabricated and Manufactured Materials (1 of 5)
- Table 6-2.1. Inspection of Fabricated and Manufactured Materials (2 of 5)
- Table 6-2.1. Inspection of Fabricated and Manufactured Materials (3 of 5)
- Table 6-2.1. Inspection of Fabricated and Manufactured Materials (4 of 5)
- Table 6-2.1. Inspection of Fabricated and Manufactured Materials (5 of 5)
- 6-203B Materials Accepted on the Basis of Authorized Materials List
- 6-203C Materials Accepted on the Basis of a Certificate of Compliance
- Table 6-2.3. Materials Accepted by Certificate of Compliance (1 of 12)
- Table 6-2.3. Materials Accepted by Certificate of Compliance (2 of 12)
- Table 6-2.3. Materials Accepted by Certificate of Compliance (3 of 12)
- Table 6-2.3. Materials Accepted by Certificate of Compliance (4 of 12)
- Table 6-2.3. Materials Accepted by Certificate of Compliance (5 of 12)
- Table 6-2.3. Materials Accepted by Certificate of Compliance (6 of 12)
- Table 6-2.3. Materials Accepted by Certificate of Compliance (7 of 12)
- Table 6-2.3. Materials Accepted by Certificate of Compliance (8 of 12)
- Table 6-2.3. Materials Accepted by Certificate of Compliance (9 of 12)
- Table 6-2.3. Materials Accepted by Certificate of Compliance (10 of 12)
- Table 6-2.3. Materials Accepted by Certificate of Compliance (11 of 12)
- Table 6-2.3. Materials Accepted by Certificate of Compliance (12 of 12)
- 6-203D Field Inspection and Release by the Resident Engineer
- 6-203A Source Inspection
Section 2 Acceptance of Manufactured or Fabricated Materials and Products
6-201 General
This section describes procedures for acceptance of manufactured or fabricated materials and products. This section also describes the types of materials that are considered manufactured materials and provides guidelines for sampling these materials.
Sampling and testing materials and products must be done in accordance with contract specifications. Sampling and testing are of equal importance for assuring materials and products meet acceptance specifications.
The contractor is responsible for notifying the resident engineer of the need for inspection and acceptance testing of manufactured materials and products by submitting Form DOT CEM-3101, “Notice of Materials to Be Used,” early in the project. Refer to Section 6-202, “Responsibilities for Acceptance of Manufactured or Fabricated Materials and Products,” of this manual for details on completing and submitting this form.
The resident engineer needs to be knowledgeable about acceptance methods used for different manufactured or fabricated materials and products, including:
- Source inspection and testing.
- Manufacturer certificate of compliance.
- Manufacturer certificate of compliance with additional attachments.
- Field release of material.
- Field samples of manufactured materials or products.
When field sampling of manufactured or fabricated materials or products is required, the resident engineer is responsible for the “chain of custody” for material and product acceptance samples. Material acceptance samples must be under the control of Caltrans from the sampling point to when the sample is tested. The chain of custody for material and product samples is an important part of the Caltrans quality assurance program.
6-201A References
- Independent Assurance Manual: See Construction's Field Resources for Contract Administration intranet page.
Or contact IA.Service.Request@dot.ca.gov.
- Bridge Construction Records and Procedures Manual, Vol. 2, Engineering Services:
https://dot.ca.gov/programs/engineering-services/manuals
- California Test Methods, METS, Caltrans:
https://dot.ca.gov/programs/engineering-services/california-test-methods
- American Association of State Highway and Transportation Officials (AASHTO), American Society for Testing and Materials (ASTM) International, and other test methods may be accessed for free with a Caltrans email address from the Material Standards (ASTM/AASHTO) link on the Division of Engineering Services' internal METS website.
- J2 Database, METS, Structural Materials electronic materials management database where each project’s test results and Form DOT CEM-3101, "Notice of Materials to be Used," responses are captured along with other METS project-related information and accessible by Caltrans staff. Staff may navigate to the J2 database on the Division of Engineering Services internal METS website.
- Material Plant Quality Program (MPQP), Division of Construction:
https://dot.ca.gov/programs/construction/material-plant-quality-program
- Quality Management System, METS, Structural Materials, methods and procedures to provide consistent quality assurance and source inspection. Staff may navigate to the Quality Assurance and Source Inspection Manual on the Division of Engineering Services' internal METS website at:
https://des.onramp.dot.ca.gov/materials-engineering-and-testing-services-mets/office-quality-assurance-source-inspection-oqasi
- Overhead Sign Structures Guide, on the Division of Engineering Services' Signs & Overhead Structures intranet page.
6-202 Responsibilities for Acceptance of Manufactured or Fabricated Materials and Products
The following describe the responsibilities for acceptance of manufactured or fabricated materials and products.
6-202A Contractor
The contractor is responsible for providing materials that comply with the contract specifications. The contractor is responsible for the quality of materials and, if required by the specifications, must provide a notice of materials to be used, shop drawings, certificates of compliance, mill test reports, environmental product declarations, quality control plans, and quality control test results. The contractor must use materials from Authorized Materials Lists, provide fabricated materials from audited facilities, and use materials that comply with Buy America and specified Buy Clean California Act requirements.
6-202A (1) Notice of Materials to Be Used
The contractor is responsible for submitting Form DOT CEM-3101, “Notice of Materials to Be Used,” to the resident engineer for all materials to be used on the project. The contractor must provide sufficient notification to the resident engineer on the source, location, and quantity of materials to be inspected and tested so that the work will not be delayed. Section 6, “Control of Materials,” of the Standard Specifications requires the contractor to list on Form DOT CEM‑3101 all sources of materials and where these materials are available for inspection. Receiving this form in a timely manner is critical to the success of the materials management process.
Form DOT CEM-3101, which includes detailed instructions, is available at:
https://dot.ca.gov/programs/construction/forms
6-202A (2) Certificates of Compliance, Mill Test Reports, Buy America and Buy Clean California Act Requirements
The specifications require the contractor to submit a certificate of compliance for various materials before they are incorporated into the work. Section 6-2.03C, “Certificates of Compliance,” of the Standard Specifications states that when a certificate of compliance is required it must be:
- Submitted for each lot of material and clearly indicate which lot is included in the certificate.
- Signed by the producer of the material stating that it complies with the contract.
The intent of the certificate of compliance is to communicate to Caltrans that the contractor has accepted the material and is confident that it complies with the contract specifications. The contractor is responsible for providing the certificate of compliance before incorporating material into the project. The certificate of compliance and any supporting documentation must accompany the material to the job site when materials are delivered.
Table 6-2.3, “Materials Accepted by Certificate of Compliance,” in Section 6-203C, “Materials Accepted on the Basis of a Certificate of Compliance,” of this manual provides a list of materials requiring a certificate of compliance, as well as any additional documents.
The specifications require the contractor to provide certified test reports along with the certificate of compliance for various materials. For steel, this test data is commonly known as a mill test report. A certified mill test report is required for each heat and must contain physical and chemical analysis of the material. The requirements for the mill test report vary depending on the section of the specifications the material falls under.
Section 6-1.04, “Buy America,” of the specifications provides detailed information on Buy America requirements. Refer to Section 3-604, “Buy America,” of this manual for additional information. The following are examples of acceptable language included in the certificate of compliance to verify Buy America compliance for steel and iron materials:
“All melting and manufacturing processes for the product occurred in U.S.”
“100 percent melted and manufactured in the U.S.A.”
The following is an example of acceptable language included in the certificate of compliance to verify Buy America compliance for construction materials, such as nonferrous metals, plastic- and polymer-based products, glass, lumber, or drywall:
“All production processes for the product occurred in U.S.”
Section 6-1.06, “Buy Clean California Act,” of the specifications provides detailed information on Buy Clean California Act requirements including environmental product declarations. Refer to Section 3-606, “Buy Clean California Act,” of this manual for additional information.
6-202A (3) Shop Drawings
The Standard Specifications requires the contractor to submit shop drawings for review by Caltrans for certain structures such as structural steel and structural precast concrete. The shop drawings must include both shop details and erection plans. For more information on submittal and authorization of shop details and erection plans, refer to the Standard Specifications.
Contractors must submit shop drawings for overhead sign structures. For more information on submittal and authorization of shop drawings, refer to the Overhead Sign Structures Guide. Section 4-56, “Overhead Sign Structures, Standards, and Poles,” of this manual contains additional information.
Before Caltrans performs any source inspection, the contractor is required to have a copy of the authorized shop drawings at the location of inspection.
6-202A (4) Quality Control Plans
The Standard Specifications requires the contractor to submit a quality control plan for certain types of production. Information on quality control plans for those production types is provided in the Standard Specifications:
- Section 11-2, “Welding Quality Control.”
- Section 39-2: “Hot Mix Asphalt.”
- Section 40: “Concrete Pavement”
- Section 41-9: “Individual Slab Replacement with Rapid Strength Concrete”
- Section 56-2: “Overhead Sign Structures”
- Section 59-2: “Painting Structural Steel”
- Section 59-5: “Thermal Spray Coat Structural Steel”
- Section 90-4: “Precast Concrete”
The resident engineer does not allow work to begin until the quality control plan is authorized for that production. For more information on the contents of quality control plans, refer to the Standard Specifications.
Specifications for welded products usually require the contractor to submit the fabricator’s welding quality control plan to the resident engineer for authorization before any products are manufactured for Caltrans. For details on quality control plans for welding, refer to Section 11, “Welding,” of Bridge Construction Records and Procedures Manual, Vol. 2:
https://dot.ca.gov/programs/engineering-services/manuals
6-202B Resident Engineer
The resident engineer must verify that materials entering the work comply with the requirements in the contract specifications.
6-202B (1) Notice of Materials to be Used
The resident engineer must verify that the contractor submits Form DOT CEM-3101, “Notice of Materials to Be Used,” for all materials. If the contractor does not submit Form DOT CEM-3101 before the preconstruction conference, provide a list to the contractor during the preconstruction meeting of materials required to be listed on Form DOT CEM-3101.
If the sources of all materials are not known, the contractor may submit a partial list of materials sources on Form DOT CEM-3101 and submit Form DOT CEM-3101 supplements as soon as other sources are known.
METS developed the J2 database for tracking project materials requirements, Form DOT CEM-3101 processing, materials test results, and source inspection. Entering the contract number at the top of the database in the “Projects” box opens that project’s main page. Clicking on the “3101 Report” tab opens a list of all the bid items requiring Form DOT CEM-3101 for the project and which Form DOT CEM-3101s have been received. The list shows the name and address of the supplier and the date the Form DOT CEM-3101 was received.
Assistance in developing a list of project materials that require Form DOT CEM-3101 and in navigating the J2 database is available from the Materials Engineering and Testing Services (METS) representative for the project:
https://dot.ca.gov/programs/engineering-services
The contractor’s submitted Form DOT CEM-3101 must include the following information:
- The contract number and the contract items for which the material will be used. If the contractor uses a project number different from the Caltrans contract number, include that number.
- The item component name and quantity.
- The name, address, and telephone number of the manufacturer.
- The name, address, and telephone number of the supplier or manufacturer where the material can be inspected.
- If the source of material is outside California, also include the name, address, and telephone number of the contractor or subcontractor placing the order and the order number.
Check Form DOT CEM-3101 for the required information and for completeness. To make sure that all structural materials are listed, a list of materials necessary based on contract bid item is available at:
https://mets.dot.ca.gov/j2_item_categories.php
If the contractor’s Form DOT CEM-3101 is incomplete or incorrect, require the contractor to complete the form. When the contractor’s Form DOT CEM-3101 has been reviewed and is complete, promptly distribute Form DOT CEM-3101 copies, including one to METS. The resident engineer sends Form DOT CEM-3101 to the materials administrator using one of the following methods:
- Email: MaterialsAdministratorMETS@dot.ca.gov
- Fax: (916) 227-7084
- Postal mail:
Materials Administrator, Mail Station #5
Materials Engineering and Testing Services
5900 Folsom Blvd, Room 517
Sacramento, CA 95819
METS will make required assignments for sampling, testing, and inspection of materials as noted in Section 6-202C, “Materials Engineering and Testing Services,” of this manual.
6-202B (2) Job Site Materials Inspection
Based on assignment of materials inspection from METS to the resident engineer and the information shown on Form DOT CEM-3101, the resident engineer must identify the appropriate district samplers, testers, and inspectors. Following is a partial list of those who may need to be notified to perform material acceptance:
- District staff who will be obtaining samples and tests of each material
- District staff who will be obtaining samples for each material accepted on the basis of a certificate of compliance. Testing is normally done by METS
- Structure Construction for reviewing and authorizing shop drawings for overhead sign structures
- District weights and measures coordinator for inspecting materials plants in accordance with the MPQP
6-202B (3) Authorized Facility Audit List
Some structural materials such as structural precast concrete, overhead signs and poles, and steel pipe piling must be fabricated at a facility on the authorized facility audit list of fabricators who have successfully completed Caltrans’ facility audit. If these materials are included in the scope of work, make sure that the contractor is aware of these requirements. Information on the authorized facility audit list is available at:
https://dot.ca.gov/programs/engineering-services/
6-202B (4) Materials Production Plants
The resident engineer must assure materials production plants meet specifications before they produce material for Caltrans. Request assistance from the district weights and measures coordinator for inspecting materials plants including:
- Hot mix asphalt plants
- Concrete plants
- Volumetric proportioning plants for rapid strength concrete, polyester concrete, and pavement seal coats
Section 9-1.02, “Measurement,” of the Standard Specifications indicates the general requirements for weighing, measuring, or metering devices and the requirement to place security seals on material plant controllers. The district weights and measures coordinator will follow the MPQP Manual and the contract specifications for material plant authorization.
6-202C Materials Engineering and Testing Services
The Materials Engineering and Testing Services (METS) assigns personnel for sampling, testing, and inspecting manufactured materials and products, usually at the source of supply. Manufactured materials and products shown in Table 6-2.3., “Materials Accepted by Certificate of Compliance,” in Section 6-203C, “Materials Accepted on the Basis of a Certificate of Compliance,” of this manual, are the responsibility of METS but have been delegated to the resident engineer for inspection.
METS assigns the responsibility for sampling, testing, and inspecting manufactured materials and products based on the information submitted on Form DOT CEM-3101, "Notice of Materials to be Used." METS offices in Sacramento, the San Francisco Bay Area, or Los Angeles conduct most of the inspections. METS may assign sampling, testing, and inspecting of manufactured materials and products to the district materials engineer, resident engineer, or a commercial laboratory.
The METS process for inspecting and releasing manufactured or fabricated materials or products is shown in Figure 6-2.1., “Inspection and Release Flowchart—Source Inspection.”
Figure 6-2.1. Inspection and Release Flowchart—Source Inspection
6-202C (1) Processing Form DOT CEM-3101
Once Form DOT CEM-3101 is received by the materials administrator, it is routed to the appropriate METS office for processing. Any questions regarding Form DOT CEM-3101 processing by METS may be routed to the project METS representative. Structural materials listed on Form DOT CEM-3101 are processed by the quality assurance and source inspection (QASI) office assigned to that project.
6-202C (2) Form TL-28, “Notice of Materials to Be Inspected at Job Site”
If it is determined that the material does not require source inspection, METS will assign inspection to the job site by completing Form TL-28 for that material item. This form indicates that the material item does not require source inspection from Caltrans at this time. METS will send Form TL-28 to the resident engineer, prime contractor, and suppliers to inform them that source inspection is not required before shipment to the job site.
The resident engineer will release these materials at the job site using Form DOT CEM-4102, “Materials Inspected and Released on Job.” Section 6-3, “Field Tests,” of this manual contains details on testing that occurs at the job site. Depending on the material, the resident engineer bases the field material acceptance on various methods. Refer to Section 6-203D, “Field Inspection and Release by the Resident Engineer,” of this manual for the field inspection and release procedures.
6-202C (3) Form TL-608, “Notice of Materials to Be Furnished”
If it is determined that the material requires source inspection before shipment to the job site, METS will issue Form TL-608 to the resident engineer, contractor, and supplier. A hard copy of Form TL-38, “Inspection Request,” is mailed with Form TL-608 to the supplier. The inspection request form is to be used by the contractor or any subcontractors to inform METS when the material is ready for inspection.
Source inspection by Caltrans is described in Section 6-202C, “Materials Engineering and Testing Services,” of this manual and is detailed in the Office of Quality Assurance and Source Inspection's QASI Manual:
https://j2.dot.ca.gov/qs/?tab=2&sdiv=METS&off=OSM
6-202C (4) Form TL-38, “Inspection Request”
Form TL-38 is used by the contractor or supplier to inform Caltrans that material located away from the job site is ready for inspection. If the contractor has received a Form TL-608 for an item, Caltrans will be expecting a Form TL-38 to initiate the source inspection.
Form TL-38 and instructions for submitting the request are available at:
https://j2.dot.ca.gov/qs/?tab=2&sdiv=METS&off=OSM
It is important to remind the contractor that, in accordance with Section 6-2.01E, “Material Source Inspection and Testing,” of the Standard Specifications, the inspection request must be submitted:
- At least 3 business days before the requested inspection date for a material source within California.
- At least 5 business days before the requested inspection date for a material source outside California but within the U.S.
- Fifty days before the planned production start for a material source outside the U.S. and notify the resident engineer at least 20 days before the actual start.
The resident engineer may also use Form TL-38 to request field inspection by METS for structural items such as field welding.
6-202D Assignment to Resident Engineer
METS may assign inspection of manufactured or fabricated materials and products for which they have acceptance responsibility back to the resident engineer. Refer to Section 6-203D, “Field Inspection and Release by the Resident Engineer,” of this manual for details on inspection and release.
6-203 Manufactured or Fabricated Materials and Products Acceptance
The resident engineer must verify that materials entering the work meet the contract specifications acceptance criteria. Materials acceptance can be based on:
- Source inspection
- Product on Authorized Materials List
- Certificate of compliance
- Certificate of compliance with accompanying documents
- Field inspection and release by the resident engineer
If the material delivered to the job site lacks proper identification, the report of inspection is unconfirmed, or the acceptability of the material is questionable, do not allow materials to be incorporated in the work until they have been found to comply with the specifications. Contact the assigned inspection unit to verify testing or submit samples for new acceptance tests.
6-203A Source Inspection
METS is responsible for the source inspection process shown in Figure 6-2.2., “Source Inspection Flowchart.” The flowchart includes information on what happens when a material is not in compliance with the specifications, prompting use of a TL-15, “Quality Assurance Nonconformance Report.”
When a material listed on Form DOT CEM-3101 is assigned a Form TL-608, source inspection is required before the material to the job site. Table 6-2.1., “Inspection of Fabricated and Manufactured Materials,” provides a list of common materials on Caltrans projects and some of the primary source inspection activities. Table 6-2.1. follows Section 6-203A (5), “Source Inspected Materials Acceptance,” of this manual.
A METS inspector will travel to the source of the material and perform inspection, sampling, verification testing, and material release as necessary. Complex fabrication, such as with precast prestressed concrete members and structural steel, typically requires inspection during fabrication.
METS must receive all information that could affect materials that are source inspected. Forward all copies of authorized shop drawings as well as notification of approved change orders to the METS representative for the project. Forward to METS copies of approved shop drawings without established distributions, for example, buildings or small structures, and notification of approvals, such as paint color, or change orders. METS should receive copies of all correspondence with contractors or suppliers that may affect the fabrication.
Figure 6-2.2. Source Inspection Flowchart
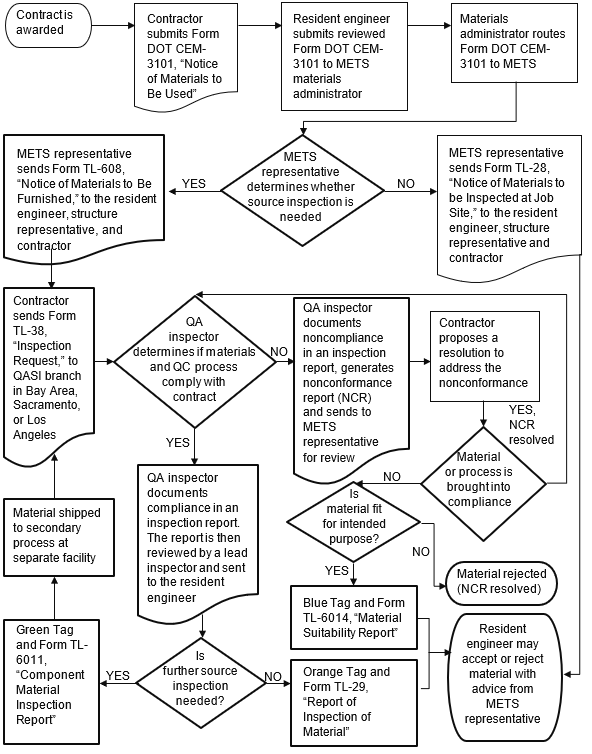
Some inspections require out-of-state travel. It is important for METS to receive all documents before travel to assure timely inspection and release. For instance, light poles are manufactured at suppliers throughout the U.S.; therefore, it is crucial that authorized shop drawings are available for the METS inspector in time for inspection and release. The travel time for such inspections is significant. Coordination between resident engineer and METS is crucial for timely release of the poles.
In addition to source inspection, METS performs sampling and testing for certain materials for conformance with associated standards as a part of the quality assurance program. The list of additional tests performed by METS is available in detail in the Office of Quality Assurance and Source Inspection's QASI Manual.
The main point of contact for the resident engineer for anything related to source inspection is the METS representative assigned to the project. A list of METS representatives is available at:
https://dot.ca.gov/programs/engineering-services/
6-203A (1) Inspection Requests and Dispatching
The contractor is responsible for submitting Form TL-38, “Inspection Request,” to the appropriate METS QASI office with sufficient notice as described in Section 6-2.01E, “Material Source Inspection and Testing,” of the Standard Specifications. The appropriate office to send Form TL-38 is available on the METS website:
https://j2.dot.ca.gov/qs/?tab=2&sdiv=METS&unitonly=1&s_tab=smforms&off=OSM
This website allows the contractor to determine the appropriate QASI office by district. The TL-38 can come from the contractor or subcontractors.
Each QASI office has a dispatcher who receives Forms TL-38 and schedules inspections.
6-203A (2) Material Inspection—Sampling and Release
The METS representative assists the resident engineer with management of source-inspected materials. The METS inspector acts as the eyes and ears of the METS representative and resident engineer at the material’s source. Inspected materials are identified with a unique inspector lot number that correlates the material with reports and release tags.
The METS inspector assesses the source’s quality control methods and reviews the certificates of compliance and any additional documentation such as mill test reports. The METS inspector also performs random visual inspection of the material and any other required inspections such as nondestructive testing. For more information on the types of inspection required for common materials, refer to Table 6-2.1., “Inspection of Fabricated and Manufactured Materials,” of this manual and the QASI Manual.
If sampling of the material is required at the source, the METS inspector will randomly sample the material at the required frequency and fill out a TL-0101, “Sample Identification Card,” to accompany the material to the Transportation Laboratory. Sampling may be performed in the field by either the METS inspector or field construction staff. The material’s certificate of compliance and any additional documents must be sent with the material to the lab as well. If the material is undergoing mechanical testing, the resident engineer can track the testing progress by using the J2 database and clicking on the “SMTL Test Reports” tab for the project.
If the material is found to be acceptable, the inspector identifies it with Form TL-0624, “Inspection Release Tag,” commonly known as an orange tag. METS inspectors will not necessarily tag every bundle and piece in a shipment. If there are many components going out in one shipment, it is common that a single orange tag will be placed on the load. The orange tag will correlate to the certificate of compliance and bill of materials with the inspector’s unique lot number. This tells the resident engineer what material the tag covers.
After the material is orange-tagged for release, the METS inspector enters the lot number, a description, and quantity of materials inspected on Form TL-29, “Report of Inspection of Material.” A completed copy of Form TL-29 is sent to the resident engineer for the project records.
Certain materials are included in the METS authorization-to-deliver program. Source inspection for these materials is different from typical procedures in that it includes a recurring audit at a prescribed frequency, with material sampling and testing. If the facility is approved to be in the authorization-to-deliver program, it is authorized to ship material to the job site without receiving a physical tag for the material. A Form TL-29AD, “Report of Inspection of Material (Authorization to Deliver),” is produced by METS and sent to the resident engineer and the supplier notifying them that the material is acceptable to be shipped. The resident engineer should not expect to obtain a tag from the material if a Form TL-29AD report was received. However, the resident engineer should match the Form TL-29AD report with the actual shipped material quantities and certificate of compliance to verify that the material arrives within a reasonable timeframe.
When source-inspected materials arrive on the job site, the attached Form TL‑0624 informs the resident engineer to permit use of the materials. The attached form shows the identifying lot number, the inspector’s initials, and the date of inspection. If the item does not lend itself to attaching of tags, such as reinforced concrete pipe, the inspector marks the lot number on each separate piece. In some instances, when there is a possibility of losing tags, the inspector both attaches tags and marks a lot number on the pieces. METS inspectors will not necessarily tag every bundle and piece in a shipment, with the exception of reinforced concrete pipe.
It is important to note that the resident engineer must inspect the materials for damage that may have occurred during shipping or storage and for general quality of work and conformance to planned shape or dimensions. Table 6-2.1., “Inspection of Fabricated and Manufactured Materials,” of this manual provides examples of types of field inspections for common materials.
The resident engineer may not receive the completed Form TL-29, “Report of Inspection of Material,” until after the materials have arrived at the job site. The resident engineer must check that the correct material was shipped to the job site by verifying that the lot number and quantity of material shown on Form TL-29 matches the identifying information, such as Form TL-0624, that was attached to or marked on the materials. Notify the project METS representative of any discrepancies so that an investigation can be conducted.
The resident engineer must inform the assigned METS inspection office if Form TL‑29 is not received within 15 days after receipt of materials.
For inspections made during fabrication, METS will produce an inspection report, unique to the type of inspection, and distribute it to the resident engineer for review and incorporation into the project files. More information on the various types of inspection reports is in the QASI Manual.
6-203A (3) Nonconforming Materials at the Source
If the inspector observes that the material does not comply with the specifications at the requested time of release, the manufacturer or fabricator is notified and allowed one work shift to correct. If the material cannot be brought into conformance within the time period, METS will send a TL-15, “Quality Assurance Nonconformance Report,” (NCR) to the resident engineer within 24 hours of the observation. The resident engineer then notifies, in writing, the contractor of the NCR and requests a written response to resolve the issue.
The purpose of the NCR is to formally document the reason the material does not meet the specifications and to prompt the contractor to propose resolution and prevention measures in the response letter. This report is entered into the J2 database under the “Issues” tab so that the information is available to Caltrans staff outside the project to help avoid future issues statewide.
When the resolution letter is submitted by the contractor, the resident engineer and METS will perform a review. If the resolution is insufficient, the contractor will be notified and allowed to revise the letter and resubmit. If the resident engineer decides that the material is not suitable for the project, it will be rejected and prohibited from incorporation into the project.
If the letter is found to be acceptable, METS will issue a TL-16, “Quality Assurance‑Nonconformance Resolution,” to the resident engineer recommending a resolution and closure of the issue. In some cases, the material is found to be suitable for the intended purpose by the resident engineer, METS, and the engineer of record for project design, but it does not meet the contract specifications. In this case, METS will produce a TL-6013, “Material Suitability Documentation Report,” to document the engineering judgment used to determine the material to be suitable and concurrence from the resident engineer, METS, and engineer of record for project design. Once authorized, the material can be released by the inspector by placing a TL-0625, “Material Suitability Tag,” referred to as a blue tag onto the material in a similar fashion as with an orange tag. A TL-6014, “Material Suitability Report,” is written in place of a TL-29, “Report of Inspection of Materials,” and sent to the resident engineer.
- When METS and the resident engineer disagree about whether the material is suitable or unsuitable, the METS Structural Materials senior engineer and the construction engineer discuss and resolve the disagreement. When consensus is not achieved at this level, the issue must be elevated to the appropriate supervisors and a mutual solution reached.
- The blue tag is only a release of the material from the source. The resident engineer may need to prepare a change order to address acceptance of the material. Section 5-303, “Purpose of Change Orders,” of this manual includes guidance for deciding whether a change order is needed. When a change order is needed, it must be approved before the material is incorporated into the work. The resident engineer sends METS copies of approved change orders addressing blue tag issues. The project’s materials certification memorandum must include material that is approved for use but does not meet original contract specifications.
6-203A (4) Source Inspection Expense Deductions
Because of costs incurred by Caltrans when traveling for source inspection to material sources that are far from the job site, Section 6-2.01E, “Material Source Inspection and Testing,” of the Standard Specifications provides the details for deductions to be taken when applicable. To determine where inspections have taken place for a project, the resident engineer can review the inspection reports that provide inspection locations.
6-203A (5) Source Inspected Materials Acceptance
The resident engineer and METS share the responsibility for inspection of materials at the source. The resident engineer has the sole responsibility for acceptance of material and may determine that materials are not acceptable for a project based on any of the following reasons:
- Damaged materials: The material may be damaged in shipment or installation.
- Material defects: It is not always practical for METS to make a 100 percent piece-by-piece inspection. The inspection is usually random sampling. The resident engineer or assistant resident engineer should check for visually detectable defects or damage.
- Incorrect wall thickness of metal culvert pipe: A given size of metal culvert pipe may vary in required thickness at various locations with different fill heights. METS inspectors cannot guarantee that a given piece of pipe will be placed at the proper location. They can only check the pipe for specified markings and determine that the measurement is within tolerance for the indicated thickness. Fit of band couplers should also be checked at the job site.
- Incorrect reinforced concrete pipe wall thickness: Some contracts require special wall thickness of reinforced concrete pipe at certain locations in the project, and the METS inspector would not know the specific job site location of that particular pipe when the pipe is released. The inspector can only determine that it fits one of the types specified.
- Specifications and change orders: The specifications may be difficult to interpret or the source inspector is not aware of a change order.
Another situation not controllable by inspection at the source is the transfer of materials from one contract to another. The inspector can confirm in the original inspection report that a given amount of material with a given lot number was inspected for the first contract. Identifying the material as that received on the first job under the original inspection report and monitoring its transfer from one job to another are responsibilities of the resident engineers involved. Such transfers should not be allowed unless the material is positively identified or is of a type, such as fencing or reinforcing steel, that can be resampled and retested in the event identification is lost or is questionable.
Table 6-2.1., "Inspection of Fabricated and Manufactured Materials," lists manufactured or fabricated materials and products that are usually inspected at the site of manufacture or fabrication and indicates items that are checked by the inspector at the source. Table 6-2.1. also includes items that must be checked or rechecked at the job site to assure that the materials are acceptable. The table does not cover all manufactured or fabricated materials and products but provides typical examples. Verification at the source of fabrication does not preclude acceptance by the resident engineer at the job site. For more details on the inspection procedures, refer to Section 6-3, “Field Tests,” of this manual, and the QASI Manual.
6-203A (6) Materials Manufactured to Caltrans-Specified Formulation
The specifications require that certain products be manufactured to state specifications. Occasionally, composition of the specified formulation is changed and the newer specification results in an equal or better product. Materials manufactured under specifications newer than those that apply to a particular project are acceptable for use. METS inspectors release such materials, and resident engineers may permit use of such materials without change orders unless specifically advised to the contrary. State specification numbers for manufacturer materials are shown in the Standard Specifications or special provisions.
Paint manufactured under state specifications is sampled at the factory, tested by METS, and identified by lot numbers before shipment to the project.
Table 6-2.1. Inspection of Fabricated and Manufactured Materials (1 of 5)
Product |
Items Inspected and Tested by METS |
Items to Check at Job Site |
---|---|---|
Bolts, nuts, and washers |
Material sampling and testing including galvanizing, visual inspection. |
Visible defects, dimensions, threads, galvanizing, marking for correct type fit of nuts. Make sure high-strength bolts and nuts are used where specified and nuts are lubricated properly. Refer to the Bridge Construction Records and Procedures Manual. |
Curing compound, chlorinated rubber type |
Material tests by batch or lot, check marking. Other types accepted at job site if properly packaged and labeled. |
Proper mixing, marking, check sample. Check for specified type of container and correct marking. |
Bearing, elastomeric bearing pads—steel reinforced, PTFE bearing (see Note) |
Material sampling and specified tests, visual and dimensional inspection certification. |
Damage, defects, uniformity, dimensions. |
Electrical items: controllers, luminaires, signal heads, conductors |
Controllers: complete tests and inspection. |
Shipping damage, defects, conformance to plans, type, operational check. Check loop detectors for operation under field conditions inspection. See that all conductors are correct type and size. |
Epoxy |
Materials sampling and specified tests, markings, packaging. |
Proper material for intended use, excessive thickening or crystallization, proper mixing. |
Forgings, steel |
METS inspection and tests upon request from resident engineer. Material tests, visual and dimensional inspection. |
Size, uniformity, surface defects, warping (permit no repairs). |
Girders, precast prestressed concrete |
Material verification, work quality, dimensions, conformance to plans, and in-process inspection of fabrication such as for forms, steel placement, stressing, and concrete stages. |
Damage, flaws, exposed steel dimensions, finish, cracks, or other defects. |
Table 6-2.1. Inspection of Fabricated and Manufactured Materials (2 of 5)
Product |
Items Inspected and Tested by METS |
Items to Check at Job Site |
---|---|---|
Girders, structural steel |
Material verification, check sample testing, qualifications of welders, inspection during fabrication, nondestructive testing, preparation and painting in the shop, conformance to plans and authorized shop drawings, proper joint preparation for shop-bolted connections. |
Damage to members or paint: defects in steel, camber condition of paint, dimensions, condition of holes, straightness and squareness of members. |
Joint sealant, Type A field mixed polyurethane or silicone sealant
|
Material sampling and testing by batch or lot. |
Proper components, proper mixing, marking. Damage, work quality, correct movement range from test report, size and type, lot and batch identification. Refer to the Bridge Construction Records and Procedures Manual. |
Joint seal, Type B preformed elastomeric joint seal |
Material sampling and testing. |
Damage, work quality, correct movement range (from test report), size and type. |
Markers, pavement |
Tests of each batch or lot, random inspection. |
Damage, surface defects. |
Mechanical equipment, scales, pump truck inspection stations, roadside rests |
Inspection usually assigned to resident engineer. Consult with Structures & Engineering Services, Office of Electrical, Mechanical, Water and Wastewater Engineering, for assistance if required. |
Damage, installation details, work quality. |
Table 6-2.1. Inspection of Fabricated and Manufactured Materials (3 of 5)
Product |
Items Inspected and Tested by METS |
Items to Check at Job Site |
---|---|---|
Metal beam guard rail |
METS inspection and testing of galvanizing upon request by resident engineer. |
Damage to rail or galvanizing, flaws of rail and galvanizing, dimensions, conditions of holes, for example. |
Metal crib wall |
METS inspection and testing of galvanizing upon request by resident engineer. |
Dimensions, work quality, galvanizing, specified bolts. |
Miscellaneous iron and steel, miscellaneous bridge metal, bearing assemblies, rings and covers, frames and grates |
Materials sampling and testing as specified, qualification of welders, inspection of fabrication, galvanizing, dimensions. |
Damage, welding or fabrication defects, conformance to drawings, galvanizing defects, grinding specified coating. |
Paint |
Materials sampling and testing by batch or lot. |
Lumps, hard setting, color, marking of cans, adherence, surface preparation, lot numbers (same as on inspection report). |
Piling, precast prestressed concrete |
Material verification, work quality, dimensions, conformance to plans, and in-process inspection of fabrication, such as forms, steel placement, stressing, and concrete stages. |
Damage, flaws, such as cracks, and spalling, painting of strand ends, straightness. |
Piling, steel pipe |
Material verification, weld inspection of welding if field splices are necessary. |
Damage to members, overlooked fabrication details, dimensions. |
Pipe, galvanized |
Material sampling and testing. Check galvanizing thickness. |
Size, uniformity, surface defects; permit no repairs. |
Poles, lighting |
Material verification, inspection and review of welding and galvanizing, visual and dimensional inspection. |
Dimensions, welds, work quality, galvanizing type. |
Table 6-2.1. Inspection of Fabricated and Manufactured Materials (4 of 5)
Product |
Items Inspected and Tested by METS |
Items to Check at Job Site |
---|---|---|
Prestressing strand |
Material sampling and testing, package and storage, visual inspection when possible. |
Check strand for rust, damage, surface defects. Check tags for stressing information. |
Reinforced concrete pipe |
Material verification, witness testing, visual inspection, dimensions, elliptical steel markings. Only for reinforced concrete pipe with diameter greater than 60 inches, unless requested by resident engineer. |
Damage, defects, exposed steel, dimensions at specific locations in accordance with plans, straightness, concentricity. |
Railings, barriers Bridge railing, barrier |
Material tests, welder qualifications, welding and fabrication, galvanizing. |
Damage to rail or galvanizing; fabrication or galvanizing defect, fit of sleeves, dimensions; types of bolts or nuts furnished. |
Reinforcement splices: welded or mechanical couplers |
METS sampling and testing, material verification. |
Refer to the Bridge Construction Records and Procedures Manual. |
Sign structures |
Material verification, qualification of welders, inspection during and after fabrication, dimensions, cleaning and painting or galvanizing. |
Damage, general work quality, general conformance to requirements, position of sign panels, final check of electrical equipment for illuminated signs, proper nuts and bolts, properly torqued. |
Signs, changeable message |
Fabrication, operation, work quality. |
Refer to Section 4-56, “Overhead Sign Structures, Standards, and Poles” of this manual. |
Table 6-2.1. Inspection of Fabricated and Manufactured Materials (5 of 5)
Product |
Items Inspected and Tested by METS |
Items to Check at Job Site |
---|---|---|
Steel flooring and grating |
METS inspection and tests upon request from resident engineer. |
Work quality, dimensions. |
Structural steel |
Material verification, qualifications of welders, inspection during fabrication, nondestructive testing, preparation and painting in the shop, conformance to plans and authorized shop drawings, proper joint preparation for shop-bolted connections. |
Damage to members or paint: defects in steel or in welds; overlooked fabrication details; camber condition of paint; dimensions; condition of holes; proper bolts and nut markings; proper torquing; straightness and squareness of members. |
Note: polytetrafluoroethylene (PTFE)
6-203B Materials Accepted on the Basis of Authorized Materials List
The specifications identify materials that must be on an Authorized Materials List. The list is available at:
https://dot.ca.gov/programs/engineering-services/
The engineer must make sure materials or products listed in Table 6-2.2., “Materials Acceptance Based on Authorized Material Lists,” are shown on the appropriate Authorized Materials List before the material is used on the project. Materials shown on the Authorized Materials List may also require a certificate of compliance or sampling and testing for acceptance.
Table 6-2.2. Materials Acceptance Based on Authorized Materials List (1 of 3)
Material or Product |
Authorized Materials List |
---|---|
Alternative sound wall system |
|
Channelizers |
Signing and delineation materials |
Chemical adhesive Drilling and bonding dowels |
Chemical adhesives or cartridge epoxies |
Crack sealant |
Flexible pavement crack treatment material |
Concrete admixtures |
Chemical admixtures for concrete |
Concrete Cementitious material |
Cementitious material |
Concrete Innocuous aggregate |
Innocuous aggregates for concrete |
Concrete anchorage devices |
Concrete inserts |
Corrosion protection system |
Corrosion protective coverings |
Corrosion protection covering for splices |
Corrosion protective coverings |
Delineators |
Signing and delineation materials |
Detectable warning surface |
Detectable warning surface |
Earth retaining system |
Earth retaining systems |
Electrical Battery backup external cabinet |
External battery backup system cabinet |
Electrical light-emitting diode (LED) signal modules |
LED traffic signals |
Epoxy powder |
Fusion-bonded epoxy powder |
Markers |
Signing and delineation materials |
Mechanical couplers |
Steel reinforcing couplers |
Organic zinc-rich primer |
Organic zinc-rich primer list |
Pavement markers |
Signing and delineation materials |
Pavement traffic stripe and marking tape |
Signing and delineation materials |
Plastic blocks |
|
Table 6-2.2. Materials Acceptance Based on Authorized Materials List (2 of 3)
Material or Product |
Authorized Materials List |
---|---|
Post-tensioning prestressing system |
Pre-approved systems; full list and details |
Precast portland-cement-based repair material |
Precast portland-cement-based repair material |
Reflectors |
Signing and delineation materials |
Reinforcement Headed bar |
Headed bar reinforcement |
Reinforcement Resistance-butt-welded splices |
|
Retroreflective · Retroreflective sheeting for barricades · Retroreflective bands for portable delineators · Retroreflective sheeting for construction area signs · Retroreflective sheeting for channelizers · Reflectors for Type K temporary railing · Retroreflective cone sleeves · White and orange-colored retroreflective stripes for plastic traffic drums · Portable signs Type 6, retroreflective, elastomeric roll-up fabric |
Signing and delineation materials |
Signs Retroreflective sheeting |
Signing and delineation materials |
Signs Fiberglass-reinforced plastic panels |
Signing and delineation materials |
Silane waterproofing |
Silane reactive penetrating sealers |
Temporary crash cushion Sand-filled |
Highway safety features |
Table 6-2.2. Materials Acceptance Based on Authorized Material List (3 of 3)
Material or Product |
Authorized Material List |
---|---|
Temporary traffic control devices Category 2 |
Acceptable, crashworthy Category 2 hardware for work zones |
Temporary traffic control devices Category 3 |
Highway safety features |
Thread locking systems |
Anaerobic thread locking systems |
Undercoating for ungalvanized sign structures |
|
Warm mix asphalt |
Warm mix asphalt—approved technologies |
6-203C Materials Accepted on the Basis of a Certificate of Compliance
In accordance with Section 6-2.03C, “Certificates of Compliance,” of the Standard Specifications, the engineer may permit the use of certain materials before sampling and testing if accompanied by a certificate of compliance.
Acceptance based on certificates of compliance is used for products for which the industry has demonstrated a high degree of reliability in meeting specifications. METS performs a programmatic assessment on a periodic basis of materials that do not receive source inspection.
METS notifies the resident engineer when material from any producer is not acceptable on the basis of a certificate of compliance. The resident engineer must notify the contractor when material cannot be accepted based on a certificate of compliance and require submittal of samples for testing before use on the project.
Certificates of compliance should contain the following information:
- Name of company
- Lot number traceable to a specific lot
- A statement naming the applicable type and brand, and that the materials meet the requirements of the Standard Specifications, the special provisions, or both
- Contract number
- Signature of responsible officer of the company
Materials accepted based on a certificate of compliance arrive on the job site without inspection by METS and Form TL-29, “Report of Inspection of Material.” When required by the Standard Specifications or the special provisions, verify that these materials have a certificate of compliance and any required additional backup documentation, such as mill test reports for steel, pressure treating reports for timber, and concrete test reports, to show that the materials comply with the specifications. Table 6-2.3., “Materials Accepted by Certificate of Compliance,” shows materials in the Standard Specifications that are accepted based on a certificate of compliance.
In addition to the materials listed in Table 6-2.3., in accordance with Section 6-2.03C, “Certificates of Compliance,” of the Standard Specifications, a certificate of compliance is required for material produced outside the United States.
Contact the project METS representative regarding any feedback or additional detail for programmatic assessment or systematic concerns regarding certain materials types.
When material delivered with a certificate of compliance is improperly certified, or any part of it is found not to comply with specifications, reject the entire shipment and notify METS immediately.
Procedures for sampling and testing materials accepted by certificate of compliance vary depending on the material. Following are some details covering the sampling of materials accepted by certificate of compliance.
Table 6-2.3. Materials Accepted by Certificate of Compliance (1 of 12)
Material/Product |
Remarks (Including Requirements for Additional Backup Information Required with Certificate of Compliance) |
---|---|
Alternative earth retaining systems |
Must state that the supplied material complies with the index criteria for the system at the time of prequalification. |
Asphalt |
Certificates of compliance must include the following:
I hereby certify by my signature that I have the authority to represent the supplier providing the accompanying asphalt product." |
Asphaltic emulsion |
Certificate of compliance must include the following:
|
Asbestos cement pipe |
|
Asbestos sheet packing |
|
Asphalt modifier |
Test results required with each truckload. |
Asphalt rubber joint sealant |
A certified test report of the results for the required tests performed within 12 months before the proposed use. |
Backer rods |
Must include manufacturer’s statement of compatibility with the joint sealant to be used. |
Barbed wire |
|
Table 6-2.3. Materials Accepted by Certificate of Compliance (2 of 12)
Material/Product |
Remarks (Including Requirements for Additional Backup Information Required with Certificate of Compliance) |
---|---|
Blast cleaning material |
|
Bonding agent for repairing spalled surface area |
Submittal of certificate of compliance required for contracts of less than 60 working days. |
Bonding material |
|
Brick |
|
Cable-type restrainers Lock nuts |
Certificate of compliance must be submitted with a copy of each required test report. |
Cast iron pipe |
|
Cast iron maintenance access rings and covers |
|
Chemical adhesive for bonding tie bars and dowel bars in concrete pavement |
|
Chemical adhesive for structures |
Certificate of compliance must state compliance with ICBO AC58 (see Note 1) and Caltrans. Augmentation/Revisions to ICBO AC58. |
Concrete Admixture |
Certificate of compliance from the manufacturer must certify that the admixture furnished is the same as that previously authorized for the Authorized Material List. |
Concrete Cementitious material |
Certificate of compliance must include the source name and location. If the cementitious material is delivered directly to the job site, the certificate of compliance must be signed by the cementitious material supplier. If the cementitious material is used in ready-mixed concrete, the certificate of compliance must be signed by the concrete manufacturer. If blended cement is used, the certificate of compliance must include a statement signed by the blended cement supplier that shows the actual percentage of supplementary cementitious material, by weight, in the blend. |
Concrete Curing compound |
Certificate of compliance must include:
|
Table 6-2.3. Materials Accepted by Certificate of Compliance (3 of 12)
Material/Product |
Remarks (Including Requirements for Additional Backup Information Required with Certificate of Compliance) |
---|---|
Concrete Minor concrete |
Before placing minor concrete from a source not previously used on the contract, a certificate of compliance stating that the minor concrete to be furnished complies with the contract requirements, including the specified minimum cementitious material content. |
Ceramic tile |
|
Chain link fencing and railing |
Certificate required for protective coating system. |
Concrete anchorage devices |
|
Concrete pipe Circular reinforced direct design method, less than 60 inches in diameter |
Certificate of compliance must:
|
Copper pipe |
|
Corrugated metal pipe |
|
Crack sealant |
Certificate of compliance must include:
|
Crash cushions |
|
Crumb rubber modifier |
Test results required with each truckload. |
Culvert markers |
|
Delineators |
Certificate of compliance required for:
|
Table 6-2.3. Materials Accepted by Certificate of Compliance (4 of 12)
Material/Product |
Remarks (Including Requirements for Additional Backup Information Required with Certificate of Compliance) |
---|---|
Dowel bar baskets |
|
Drop inlet grates and frames |
|
Drain tile |
|
Drip irrigation line |
|
Elastomeric bearing pads Plain |
Certified test results for the elastomer. METS samples and tests bearing pads. |
Elastomeric bearing pads Steel-reinforced |
Certified test results. METS samples and tests bearing pads. |
Electrical Battery backup system |
Certificates of compliance are required for:
|
Electrical Conductor |
|
Electrical Conduit (galvanized and plastic) |
|
Electrical Equipment |
|
Electrical Pull boxes (concrete and plastic) |
|
Electrical Service cabinets |
|
Epoxy |
|
Epoxy powder coating for dowel bars and tie bars |
METS samples and tests epoxy coating. |
Erosion control |
Certificate of compliance is required for:
|
Table 6-2.3. Materials Accepted by Certificate of Compliance (5 of 12)
Material/Product |
Remarks (Including Requirements for Additional Backup Information Required with Certificate of Compliance) |
---|---|
Erosion control (continued) |
Certificate of compliance with attachments is required for:
Polymer-stabilized fiber matrix Certificates of compliance attachments include:
|
Expansion joint filler |
|
Fiberglass pipe |
Certificate of compliance must be submitted with laboratory test results. |
Filler material for repairing spalled surface areas |
Submittal of certificate of compliance required for contracts of less than 60 working days. |
Gabions |
If polyvinyl chloride (PVC) coating is shown, a suitable ultraviolet resistant additive must be blended with the PVC and the additive must be shown on the certificate of compliance. |
Geocomposite drain |
Certificate of compliance must certify that the drain produces the specified flow rate. The certificate must be accompanied by a flow capability graph for the geocomposite drain showing flow rates and the externally applied pressures and hydraulic gradients. Verification must be by an authorized laboratory for the flow capability graph. |
Geosynthetics |
Test sample representing each lot and minimum average roll value. |
Table 6-2.3. Materials Accepted by Certificate of Compliance (6 of 12)
Material/Product |
Remarks (Including Requirements for Additional Backup Information Required with Certificate of Compliance) |
---|---|
Glass beads |
Certificate of compliance by lot or batch and test data from an independent laboratory. |
Glue laminated timbers and decking |
|
Guide markers |
|
Irrigation hose |
|
Irrigation pipe |
Certificate of compliance required for:
Plastic pipe supply line for pipe with wall thickness of the bell less than the specified minimum wall thickness of the pipe |
Joint filler material |
|
Joint seals (Type A and AL) |
Certified test report for each batch of sealant. |
Joint seal (Type B) |
Certificate of compliance required for:
Certificate of compliance must be submitted with certified test report for each lot of elastomeric joint seal and lubricant-adhesive. Test reports must include the seal movement range, the manufacturer's minimum uncompressed width, and test results. METS samples and tests joint seal. |
Joint seal Alternative joint seal assemblies |
For alternative joint seal assemblies, a certificate of compliance must be submitted for each shipment of joint seal materials. The certificate must state that the materials and fabrication involved comply with the specifications and the data submitted in obtaining the authorization for the alternative joint seal assembly. METS samples and tests joint seal assemblies. |
Joint seal Joint seal assemblies |
METS samples and tests joint seal assemblies. |
Lime |
Certificate of compliance must include a statement certifying the lime furnished is the same as on the Authorized Materials List. |
Table 6-2.3. Materials Accepted by Certificate of Compliance (7 of 12)
Material/Product |
Remarks (Including Requirements for Additional Backup Information Required with Certificate of Compliance) |
---|---|
Machine spiral wound PVC pipeliners |
Certificate of compliance for each reel of PVC strip must include:
|
Markers |
Certificate of compliance required for:
|
Masonry block |
Certificate of compliance required for:
|
Micro surfacing emulsion |
|
Mulch |
|
Open steel flooring and grating |
|
Overside drains |
Certificate of compliance based on steel materials, aluminum materials or plastic materials. |
Parking area seal material |
|
Pavement markers |
|
Plastic lumber |
Certificate of compliance for each shipment of plastic lumber, that must be accompanied by a laboratory test report. |
Plastic traffic drums |
|
Plastic pipe for drainage |
Certificate of compliance must include average pipe stiffness, resin material cell classification, and date of manufacture. For corrugated polyethylene pipe, manufacturer’s copy of plant audits and test results from the National Transportation Products Evaluation Program for the current cycle of testing for each pipe diameter furnished. |
Table 6-2.3. Materials Accepted by Certificate of Compliance (8 of 12)
Material/Product |
Remarks (Including Requirements for Additional Backup Information Required with Certificate of Compliance) |
---|---|
Portable changeable message sign |
|
Precast concrete Cementitious material used in precast concrete products |
Certificate of compliance must be signed by the precast concrete product manufacturer. |
Precast concrete Box culverts |
Certificate of compliance must be signed by the manufacturer's quality control representative for each shipment. |
Precast concrete members |
Certificate of compliance is for materials incorporated in the work, and for testing and inspections that have been performed. |
Precast raised traffic bars |
|
Preformed compression seal for concrete pavement |
|
Preformed membrane sheet |
Must include type of sheet and the conditioner or primer application rates. |
PTFE bearing materials (see Note 2) |
|
Rapid strength concrete |
Certificate of compliance is required for each delivery of aggregate, cementitious material, and admixtures used for calibration tests. The certificate of compliance must state that the source of the materials used for the calibration tests is the same source as to be used for the planned work. |
Reinforcement |
You may request that the contractor submits with certificate of compliance:
|
Reinforcement Epoxy-coated |
Certificate of compliance for each shipment of epoxy-coated reinforcement must be submitted with:
METS samples and tests epoxy coating. |
Table 6-2.3. Materials Accepted by Certificate of Compliance (9 of 12)
Material/Product |
Remarks (Including Requirements for Additional Backup Information Required with Certificate of Compliance) |
---|---|
Reinforcement Epoxy-coated prefabricated reinforcement |
Certificate of compliance for each shipment of epoxy-coated prefabricated reinforcement must be submitted with:
METS samples and tests epoxy coating. |
Reinforcement Epoxy-coating patching materials |
Certificate of compliance for the patching material must include certification that the patching material is compatible with the epoxy powder to be used. |
Reinforcement Headed bar |
Certificate of compliance for each shipment of headed bar reinforcement must be submitted with: 1. Mill test reports for the: a. Bar reinforcement b. Head material 2. Production test reports 3. Daily production logs METS samples and tests headed bar. |
Reinforcement Splice material |
Certificate of compliance for each shipment of splice material must be submitted with: 1. Type or series identification of the splice material, including tracking information for traceability. 2. Grade and size number of reinforcement to be spliced. 3. Statement that the splice material complies with the type of mechanical splice on the Authorized Materials List. 4. For resistance-butt-welded material: a. Heat number b. Lot number c. Mill certificates METS samples and tests reinforcement splices. |
Sheet metal |
|
Table 6-2.3. Materials Accepted by Certificate of Compliance (10 of 12)
Material/Product |
Remarks (Including Requirements for Additional Backup Information Required with Certificate of Compliance) |
---|---|
Sign panels |
Certificates of compliance required for:
|
Silicone joint sealant |
A certified test report of the results for the required tests performed within 12 months before the proposed use. |
Slotted edge drain |
|
Snow poles |
|
Snow plow deflectors polyethylene material |
|
Soil amendment |
|
Steel crib wall |
|
Steel pipe piles |
The certificate of compliance must be signed by the plant's quality control representative. The quality control representative must be on record with Structural Materials. Certificate of compliance must include:
|
Structural plate culverts |
Certificate of compliance required for:
Metal liner plate pipe |
Table 6-2.3. Materials Accepted by Certificate of Compliance (11 of 12)
Material/Product |
Remarks (Including Requirements for Additional Backup Information Required with Certificate of Compliance) |
Structural shape steel piles |
Certificate of compliance must include a statement that all materials incorporated in the work and all required tests and inspections of this work have been performed as described. |
Structural composite lumber used in falsework |
|
Structural steel thermal spray coat Wire feedstock |
|
Styrofoam filler |
|
Subsurface drain |
|
Temporary concrete washout |
Certificate of compliance required for:
|
Temporary fence [Type environmentally sensitive area (ESA)] |
Certificate of compliance required for:
|
Temporary linear sediment barrier |
Certificate of compliance required for:
|
Temporary railing (Type K) |
|
Thermoplastic traffic stripes and pavement markings |
Certificate of compliance by lot of batch and test data report from an independent laboratory. Obtain a minimum 1-foot length of stripe test sample. |
Tie bars |
METS samples and tests epoxy coating. |
Tie bar baskets |
METS samples and tests epoxy coating. |
Timber products (treated and untreated) |
Certificate of compliance for timber and lumber must state the species of the material to be shipped and include a certified grading report. If treated, certified treating report. |
Threaded tie bar splice couplers |
|
Table 6-2.3. Materials Accepted by Certificate of Compliance (12 of 12)
Material/Product |
Remarks (Including Requirements for Additional Backup Information Required with Certificate of Compliance) |
---|---|
Turf sod |
|
Two-component paint traffic stripes and pavement markings |
Certificate of compliance by lot or batch. Obtain a 50-foot test section before application of paint. |
Underdrains |
Certificate of compliance required for:
|
Waterproofing fabric |
|
Waterstop |
Certificate of compliance for waterstop material must state compliance with paragraph 6 of Army Corps of Engineers CRD-C 572. |
Welded wire fabric |
|
Wire mesh fencing |
|
Wood Structures |
Certificate of compliance for timber and lumber stating the species of the material to be shipped and including a certified grading report. If timber is treated, include a certified treating report. Certificate of compliance for glued laminated timbers and decking. |
Notes
Note 1: International Conference of Building Officials Adhesive Anchors in Cracked and Uncracked Masonry Elements (ICBO AC58)
Note 2: polytetrafluoroethylene (PTFE)
6-203C (1) Asphalt
Certification for asphalt must comply with Caltrans’ Certification Program for Suppliers of Asphalt. Program requirements, procedures, and a list of approved suppliers, are available on the METS website:
https://dot.ca.gov/programs/engineering-services/
When asphalt arrives at the job site or at the plant accompanied by a certificate of compliance, accept the shipment for use and sample and test for acceptance during use. When shipments of asphalt arrive without certificates of compliance, sample the asphalt and do not allow use before receiving acceptance test results.
All samples of asphalt, along with the necessary forms and tickets, are sent to METS at Engineering Services. Ship sample cans two at a time, in the cardboard cartons used for shipping samples of the completed mix. Take samples in the amount and frequency shown in the tables in Section 6-1, “Sample Types and Frequencies,” of this manual.
Asphalt is very hot; therefore, for safety reasons, the acceptance samples must be sampled by the contractor. The resident engineer must witness the contractor taking acceptance samples. The resident engineer must determine when the sample is to be taken and then observe that the sample is taken in accordance with California Test 125, “Method of Test for Sampling Highway Materials and Products Used in the Roadway Pavement Structure Sections,” or sampling requirements specified in contract special provisions. Take possession of the sample from the contractor and transport it to a Caltrans office or the testing laboratory.
After obtaining a sample from a plant storage tank, write the shipment number on Form TL-0101, “Sample Identification Card.”
METS sends test results to the district materials engineer and to the resident engineer.
6-203C (2) Asphalt Rubber Latex Joint Filler
Submit samples in 1-quart friction-top cans. Sample after the contents of the drum have been stirred thoroughly and brought to a uniform consistency and before the setting powder has been added. Note the batch number and the shipment number on Form TL‑0101.
6-203C (3) Two-Component Joint Sealing Compounds
This material is usually in 2-gallon pails. Each pail requires a manufacturer’s lot number. Before sampling, stir thoroughly. Samples should be taken in the amount and frequency shown in the tables in Section 6-1, “Sample Types and Frequencies,” of this manual.
6-203C (4) Cement
For cement delivered directly to the job site by the manufacturer, require one certificate of compliance for each shipment.
A single certificate for each brand may certify the cement used in ready-mixed concrete by the vendor of the concrete, to cover all deliveries in a single day. It must show:
- The name or brand of cement
- Mill source
- The total number of cubic yards of concrete delivered under the certificate
- A complete list of individual deliveries, identified by delivery slip number or other suitable identification
A single certificate may cover all deliveries of precast products in a single lot. It must show the name or brand of cement and the length of each size of pipe or the number of precast units of other types represented.
METS inspects precast products, including pipe, made at a plant other than that of the contractors at the job site. When such inspection is complete, the resident engineer is relieved of responsibility for obtaining certificates of compliance and sampling of cement. The inspector at the precast product plant will handle cement inspection approximately as outlined for ready-mix concrete.
Certificates of compliance for cement are inspected and filed by the resident engineer. In the event of a cement test failure, forward copies of certificates to METS.
Sample cement in accordance with the frequencies shown in Section 6-1, “Sample Types and Frequencies,” of this manual, and in accordance with California Test 125, “Method of Test for Sampling Highway Materials and Products Used in the Roadway Pavement Structure Sections.”
Where plant facilities include a cement auger, the cement samples may be obtained by a pipe-sleeve sampling device or by any other convenient method.
A full 8 pounds is sampled at one time, not in smaller increments. Close the bag immediately, leaving room for the cement to shift. Place the sealed bag in a second plastic bag with the white copy of Form MR-0518, “Job Cement Samples Record.” Form MR-0518 should show the certificate of compliance serial number, cement brand and type, name of mill or vendor, date, time sampled, and contract number.
After identification, box the cement samples in corrugated cartons designed to hold single, 8-pound samples or in concrete cylinder cartons, which will hold 6 samples. Ship no more than 6 samples in any 1 container.
Mark the shipping carton “Cement Sample,” and ship it to METS.
Test reports of cement are issued by METS. Acceptability of current shipments from the mill will be shown on the report, but the reports may not actually include results of samples taken from a specific project. The test reports, however, are applicable to each contract identified on a test report. When a project has special requirements for cement, or if there are other nonroutine conditions, submit special samples with instructions that they be tested and reported for the specific project.
6-203C (5) Paint
Sample all paint in the field, except paint specified as commercial quality, and send the samples to METS for testing in accordance with the frequency shown in Section 6-1, “Sample Types and Frequencies,” of this manual.
For bridges and other major structures, do not allow the paint to be used until the test results of field samples are available. For other miscellaneous painting, properly inspected and identified paint may be used pending test results.
Send paint samples from the field to METS as soon as it is received on the project. During the progress of the job, take special check samples when the paint exhibits hard settling or if contamination of paint is suspected.
Proper sampling to obtain a representative portion of the paint is mandatory.
Use the following sampling methods:
- For bridges and other major structures, or whenever large quantities are involved, send an unopened 5-gallon bucket to METS. METS will return unused portions to the job.
- For smaller samples:
- Pour the top liquid into a clean container as large as the one being sampled.
- Stir the settled portion of the paint with a paddle, gradually reincorporating the decanted liquid until all has been added.
- “Box” the paint by pouring it back and forth between the 2 containers at least 5 or 6 times or until the paint is mixed thoroughly.
- Take a gallon sample immediately.
Send all samples to METS, along with all pertinent information. Use Form TL-0101, “Sample Identification Card.”
When the paint is Caltrans-furnished, check samples will not be required.
6-203C (6) Pavement Traffic Stripe and Marking Materials
California Test 406, “Method of Test for Field-Sampling of Pavement Marking Materials,” describes procedures for obtaining samples of pavement-marking materials from a factory-sealed bag, bulk container, or stripe-application equipment. Circumstances at the job site often affect where to gather the sample. Field-striping inspectors must follow the procedures in California Test 406 to assure that representative samples are taken of pavement-marking materials.
Field sampling must be initiated by the striping inspector or the resident engineer under the following conditions:
- The material is more than 1 year old, based on the date of manufacture.
- Product tampering or adulteration is suspected.
- Adequate proof that the product has been pretested and approved is not provided, for example, batch approval paperwork is missing or other product or batch number discrepancies on containers or paperwork.
Where large quantities of pavement-marking materials are being applied, random quality assurance sampling of these materials is advisable.
Samples of pavement-marking materials in unopened factory-sealed bags are preferred. Factory-sealed bags are labeled with the manufacturer’s name and batch number, which makes identification easier. When sampling glass beads and thermoplastic, collect the following sample quantity to assure a representative sample:
- One unopened 50-pound bag of glass beads of the same manufacturer and lot number being used in the striping operation.
- One unopened 50-pound bag of thermoplastic of the same manufacturer and lot number being used in the striping operation.
For paint, bulk containers can be sampled only when the material is first homogeneously mixed using appropriately sized mixing equipment. For bulk containers of paint, obtain a 1-quart sample. Multiple samples are necessary when sampling paint directly from the application equipment to assure that the product is homogeneously mixed. Each sample must be approximately 1 quart and submitted separately.
Label samples of pavement-marking materials according to where and how they were gathered at the job site. Include pertinent information on Form TL-0101, “Sample Identification Card,” and send samples to METS for testing.
6-203C (7) Reinforcement
Refer to Section 4-52, “Reinforcement,” of this manual for details.
6-203D Field Inspection and Release by the Resident Engineer
METS may assign inspection of manufactured or fabricated materials and products for which they have acceptance responsibility back to the resident engineer. The process to be followed for inspection at the job site is shown in Figure 6-2.3., “Inspection and Release Flowchart—Inspection at Job Site.”
Figure 6-2.3. Inspection and Release Flowchart—Inspection at Job Site
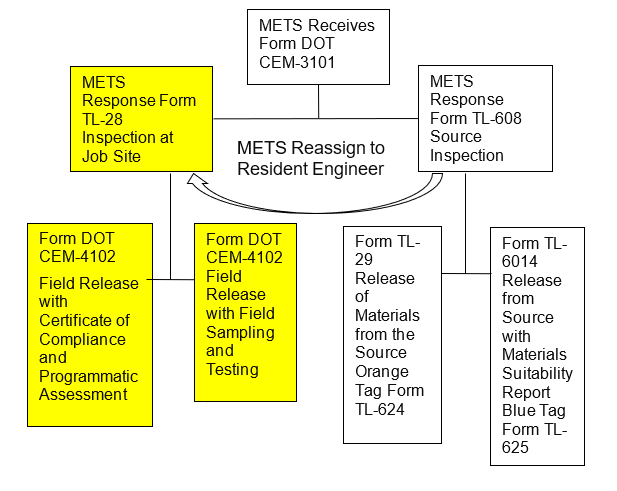
METS assigns inspection responsibility to the resident engineer using Form TL-28, “Notice of Materials to Be Inspected at Job Site.”
Upon receipt of Form TL-028, the resident engineer should inform the contractor that the material will be inspected, and if required, sampled, on the job site. When testing of material is required, inform the contractor of the approximate testing turnaround time so that the contractor can obtain the material to allow for sampling and testing before the work begins.
Materials may be accepted based on required certificates of compliance or sampling and testing and visual inspection. When material will be accepted and released at the job site by use of a certificate of compliance, the required certificate of compliance should accompany the material to the job site and be retained in the project files. Sample materials in accordance with the tables at the end of Section 6-1, “Sample Types and Frequencies,” of this manual, or as requested by METS.
Field inspect and release materials assigned by METS at the job site using Form DOT CEM‑4102, “Material Inspected and Released on Job.” Refer to Section 6-3, “Field Tests,” of this manual for details.
Construction Manual Chapters
Chapter 1 - Caltrans Construction Organization
Chapter 2 - Safety and Traffic
Chapter 3 - General Provisions
Chapter 4 - Construction Details
Chapter 5 - Contract Administration
Chapter 6 - Sampling and Testing
Chapter 7 - Environmental Stewardship
Chapter 8 - Employment Practices
Chapter 9 - Projects Sponsored by Others